-
Automatic Self Cleaning Filter
-
Self Cleaning Filter
-
Bernoulli Filter
-
Automatic Back Flushing Filter
-
Bag Filter Housing
-
Scraper Filter
-
Metal Edge Filter
-
Tubular Filter
-
Automatic Backwash Filter
-
Magnetic Trap
-
Basket Filter Housing
-
Cartridge Filter Housing
-
Solid Liquid Separator
-
Filter Element
-
JetFlow Automatic Backwash Filters
-
Mr. GustovaLIVIC is our worth-trust partner and privide us reliable filtration support.
-
Mrs. ShurkoLIVIC provide us the proper filter for our painting filtration.
304 Pneumatic Driven Self Cleaning Filter For Polymer Coatings DFA41
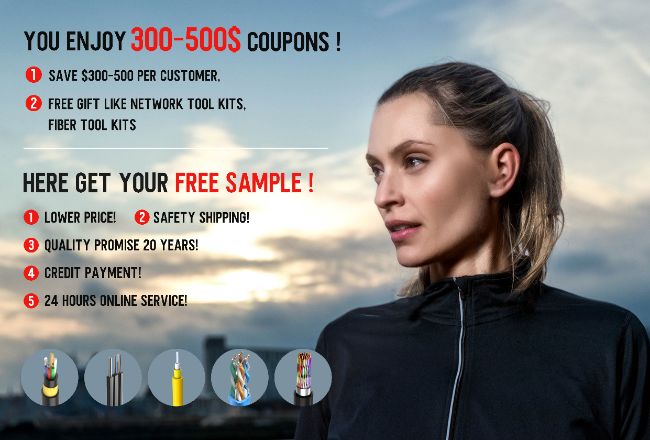
Contact me for free samples and coupons.
Whatsapp:0086 18588475571
Wechat: 0086 18588475571
Skype: sales10@aixton.com
If you have any concern, we provide 24-hour online help.
xHousing Material | Stainless Steel304/316L/Carbon Steel | Filtration Degree | 50-2000 Micron |
---|---|---|---|
Viscosity | 1-800000 Centipoise | Flowrate Rang | 10-1800 L/s |
Design Pressure | 10 Bar | Design Temperature | 200℃ |
High Light | Self Cleaning Filter For Polymer Coatings,Pneumatic 304 Self Cleaning Filter,2000 micron Self Cleaning Filter |
304 Pneumatic Driven Self Cleaning Filter For Polymer Coatings DFA41
- Elimination or reduction in disposable filter bags and cartridges for reduced operator handling inventory costs and landfill waste
- Reduction in product loss, more thorough contaminant purge in a highly concentrated waste stream
- Virtually maintenance free, near 100% uptime
- Compact design, lower capital cost to fit most installations
- Stainless steel screens from 50 micron slots to 1/4" perforations to handle a wide range of filtration needs
- Reduction or elimination of operator intervention for safer operation
Specifications:
Filter Main Type | DFA7 | DFA22 | DFA41 | DFA71 | DFA213 | DFA284 |
Filter Area(㎡) | 0.07 | 0.22 | 0.41 | 0.71 | 2.13 | 2.84 |
Filter Element Qty. | 1 | 3 | 4 | |||
Volume(L) | ~4 | ~24 | ~42 | ~175 | ~620 | ~760 |
Inlet&Outlet Size | DN25-DN50 | DN50-DN80 | DN65-DN100 | DN80-DN125 | DN100-DN150 | DN150-DN250 |
Purge Size | DN40 | |||||
Applicable Liquid | water and viscous liquid (<800000cps),impurities content<1000ppm | |||||
Standard Design Pressure | 1.0MPa,higher design pressure available | |||||
Design Temperature | 0-200℃(determined by seal materials) | |||||
Cleaning D.P. | 50-100KPa(differs by the liquid viscosity) | |||||
D.P. Instrument | pressure transmitter / differential pressure transmitter | |||||
Inlet&Outlet Standard | HG20592-2009 Flange(standard, DIN compatible ), HG20615-2009 Flange ( ANSI B16.5 compatible)DIN11851 sanitary coupling, female thread | |||||
Filter Element Series | MS/NS/AS | |||||
Housing Wet Part Material | ||||||
Piston Material | 316L | |||||
Scraper Material | PTFE | |||||
Housing Seal Material | NBR/EPDM/VITON/Silastic/FEP encapsulated Silastic | |||||
Element Seal Material | NBR/EPDM/VITON/Silastic/FEP encapsulated Silastic | |||||
Piston Rod Seal Material | NBR/PU/VITON | |||||
Purging Valve | Full-port pneumatic ball valve, single action or double action, material 304/316 | |||||
Facility Supply Requirement | 220V AC for control system, 0.4-0.6MPa clean and dry compressed air | |||||
Custom-made Design |
jacket design for thermal oil or steam, keep the temperature and fluidity ing the instruments and control system, for flammable and explosive applications
|
Liquid enters the filter from the inlet. The spring-loaded disc-shape scraper tightly fits the filter element internal surface and stops at the top of the filter element. The liquid passes the scraper and flows across the filter element from inside to outside. The impurities are blocked on the inner element surface. The liquid flows out from the outlet. After running for a period, more and more impurities accumulate and the pressure drop increases. Clean the filter element by the preset differential pressure or the preset time cycle.
The cylinder drives the scraper moving up and down and cleaning the filter element. When the scraper moving down, the impurities are pushed down to the filter bottom, and gravity particles settle down to the impurity collection chamber. When the scraper moving up, the remaining impurities are pushed to the top of the filter element and then flushed off by the liquid. The impurities pass the scraper, get back the filter element internal surface and then scraped off when the scraper moving down. Each cleaning cycle consists of several strokes. After cleaning, the filter element are regenerated. When cleaning, it filters normally and flowrate is not interrupted.
After several cleaning cycles, the impurities accumulate more and more. Open the valve periodically and purge the waste liquid of high impurity concentration, which can be recovered if necessary.
Applications:
■ Applicable Industries: petro-chemical, fine chemical, pulp and paper, food and beverage, water treatment, etc.
■ Applicable Liquid Types: wax, coal oil, monomer, polymer, citric acid, fermented broth, cosmetics, silicon solution, soap, sorbitol, steriodsugar, wet end additives, adhesives, inks, lubricating oils, coatings, resin, rubber, ethanol, miscella, edible oil, juice, diesel, etc.
TECHNICAL FEATURES AND ADVANTAGES
■Up-and-down reciprocating scraping, scrape impurities off directly, especially good at viscous liquid filtration and removing viscous suspending impurities
■Simple structure, easy disassembly, pull the filter element out easily after removing the scraper, easy for internal cleaning
■Automatic operation, continuously on-line filtration, terminate the hard work of filter element replacement and cleaning
■No disposable filter media, save the cost of filter media consumption and the environment treatment
■Very low filtration pressure drop, steady flow rate, save the energy, good for keeping the process continuous and steady
■Closed filtration, prevent danger of liquid leakage, good for safety production and operator’s health